Instalação de Compressores Industriais: Guia Completo
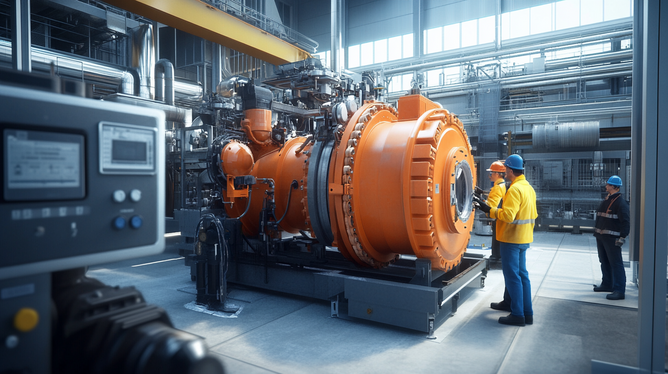
Por: Jeferson - 21 de Dezembro de 2024
A instalação de compressores industriais é um passo crucial para garantir o funcionamento eficiente de diversos processos produtivos. Ao longo deste artigo, abordaremos as principais vantagens dessa instalação, as etapas necessárias para realizá-la de forma segura, a escolha do compressor ideal para suas necessidades e a importância da manutenção após a instalação. Continue lendo para obter informações valiosas que ajudarão na sua tomada de decisão.
Vantagens da Instalação de Compressores Industriais
A instalação de compressores industriais traz uma série de benefícios significativos para as operações, tornando-se uma necessidade em muitos setores. Seja na indústria manufatureira, na construção ou em sistemas de climatização, os compressores industriais desempenham um papel vital. Neste artigo, vamos explorar as várias vantagens que a instalação de compressores industriais pode oferecer às empresas.
Eficiência Energética
Um dos principais benefícios da instalação de compressores industriais é a eficiência energética. Os compressores modernos são projetados para operar com um consumo de energia otimizado. Isso significa que, ao implementar um compressor industrial, as empresas podem reduzir significativamente seus custos com eletricidade, resultando em economia a longo prazo.
Além disso, compressores eficientes têm um impacto positivo no meio ambiente, pois consomem menos recursos e emitem menos gases poluentes. As indústrias que adotam práticas sustentáveis podem se beneficiar de uma imagem de marca mais positiva e de possíveis incentivos governamentais.
Confiabilidade e Durabilidade
Os compressores industriais são projetados para suportar condições rigorosas e operar em ambientes desafiadores. Ao serem instalados corretamente, esses sistemas oferecem uma confiabilidade superior e uma durabilidade prolongada. Isso é essencial em um cenário industrial onde o tempo de inatividade pode resultar em perdas financeiras significativas.
Compressores industriais de qualidade são construídos para resistir ao desgaste e fornecer desempenho consistente, o que significa que as empresas podem contar com eles para manter suas operações funcionando sem interrupções. A manutenção adequada, combinada com a escolha do compressor certo, aumenta ainda mais a durabilidade do equipamento.
Versatilidade de Aplicações
A instalação de compressores industriais proporciona versatilidade nas aplicações. Esses dispositivos podem ser usados em uma variedade de setores, incluindo fabricação, alimentação e bebidas, farmacêutico, construção, entre outros. Com diferentes tipos de compressores disponíveis, como os de parafuso, alternativos e centrífugos, as indústrias podem escolher o sistema que melhor se adapta a suas necessidades específicas.
Além disso, os compressores podem ser usados em diversas funções, como controle de pressão, movimentação de materiais, resfriamento e sistemas pneumáticos. Essa flexibilidade permite que as empresas otimizem seus processos e aumentem a produtividade.
Melhorias na Qualidade do Produto
Outro aspecto fundamental da instalação de compressores industriais é a melhoria na qualidade do produto. Um fornecimento constante e controlado de ar comprimido é crucial para várias operações de fabricação. Com um compressor bem instalado e mantido, as empresas podem garantir que os processos de produção sejam mais uniformes e que as especificações de qualidade sejam atendidas de forma consistente.
Nos setores de alimentos e bebidas, por exemplo, a qualidade do ar comprimido é vital para evitar contaminações e garantir a segurança do produto. Compressores industriais certificados podem ajudar a cumprir as normas e padrões de qualidade exigidos pela indústria.
Redução de Ruído
Compressores industriais mais antigos frequentemente produzem níveis elevados de ruído, o que pode ser prejudicial tanto para os trabalhadores quanto para o ambiente. Com a instalação de compressores industriais modernos, as empresas podem se beneficiar de tecnologias que reduzem significativamente os níveis de ruído. Isso não só melhora o ambiente de trabalho, mas também ajuda a atender os regulamentos de controle de ruído em áreas urbanas.
A utilização de silenciadores e uma disposição adequada do compressor pode resultar em um espaço de trabalho mais agradável e seguro. Um ambiente menos barulhento também contribui para a produtividade dos funcionários, permitindo que eles trabalhem com mais concentração.
Automatização e Controle
A instalação de compressores industriais frequentemente vem acompanhada de sistemas de automação e monitoramento. Esses sistemas permitem que as empresas controlem o desempenho do compressor em tempo real, detectando qualquer anomalia ou problema antes que se torne crítico.
Os sistemas modernos podem incluir recursos como controle de pressão, ajustes automáticos de carga e capacidade, e até mesmo integração com softwares de gestão de produção. Essa automação não só melhora a eficiência, mas também proporciona uma operação mais segura, reduzindo o risco de acidentes.
Facilidade de Manutenção
Ao optar pela instalação de compressores industriais, as empresas têm à sua disposição equipamentos que são projetados para facilitar a manutenção. Muitas unidades modernas vêm com características que permitem acesso fácil a componentes essenciais, o que simplifica processos de manutenção e reparo.
Além disso, muitos fabricantes oferecem programas de manutenção preventiva, o que ajuda a prolongar a vida útil do compressor e a garantir que ele funcione de maneira ideal. A natureza simples de manutenção dos compressores modernos representa um ganho significativo em eficiência operacional.
Custos Operacionais Reduzidos
A longo prazo, a instalação de compressores industriais pode levar a uma redução significativa nos custos operacionais. Isso se deve a fatores como a eficiência energética, baixa necessidade de manutenção e a confiabilidade dos sistemas. Menos paradas não programadas e um desempenho constante resultam em uma economia substancial, permitindo que as empresas realoquem recursos para outras áreas de crescimento.
Além disso, a redução nos custos com energia e manutenção representa um retorno sobre o investimento atraente para as empresas, ajudando a justificar os custos iniciais de instalação.
Impacto no Meio Ambiente
Em um mundo cada vez mais preocupado com as questões ambientais, a instalação de compressores industriais adequados pode contribuir para operações mais sustentáveis. Os compressores modernos são projetados para ser mais eficientes, resultando em menores emissões de gases de efeito estufa. Além disso, muitos modelos utilizam refrigerantes que têm menos impacto ambiental.
As empresas não apenas atendem às regulamentações ambientais, mas também podem se beneficiar da preferência dos consumidores por práticas sustentáveis. Isso pode resultar em uma vantagem competitiva no mercado.
Suporte Técnico Especializado
A instalação de compressores industriais geralmente é acompanhada de suporte técnico especializado. Os fabricantes e distribuidores oferecem treinamentos, manuais e suporte nas primeiras operações, o que garante que a equipe da empresa esteja capacitada a lidar com o equipamento corretamente.
Essa assistência ajuda as empresas a otimizar ainda mais o uso de seus compressores, garantindo que eles sejam utilizados da melhor maneira possível para maximizar a eficiência e a performance geral.
Conclusão
As vantagens da instalação de compressores industriais são abundantes e impactam diretamente a eficiência, a qualidade e a sustentabilidade das operações de uma empresa. Desde a redução de custos operacionais até a melhoria da qualidade do produto, a instalação correta de compressores é um investimento que pode trazer resultados significativos a longo prazo. Com o crescimento constante da demanda industrial, ter um compressor adequado se tornou uma parte essencial do sucesso empresarial em um ambiente competitivo.
Etapas para uma Instalação Segura
A instalação de compressores industriais é um processo que exige cuidado e atenção aos detalhes para garantir não apenas a eficiência do equipamento, mas também a segurança dos operadores e da infraestrutura. A seguir, descrevemos as etapas essenciais para uma instalação segura de compressores industriais, abrangendo desde a escolha do local até os testes finais após a instalação.
Planejamento e Avaliação do Local
O primeiro passo para uma instalação segura é o planejamento detalhado e a avaliação do local onde o compressor será instalado. É fundamental considerar fatores como
- Espaço disponível: O local deve ter espaço suficiente não apenas para o compressor, mas também para a circulação de ar e para a manutenção. O acesso fácil é essencial para futuras manutenções e reparos.
- Ventilação: Compressores industriais geram calor e podem ser fontes de emissões de gases, por isso um local bem ventilado é crucial para garantir a segurança e o funcionamento adequado do equipamento.
- Superfície adequada: A superfície onde o compressor será instalado deve ser nivelada e capaz de suportar o peso do equipamento, assegurando que não haja riscos de deslizamento ou tombamento.
Escolha do Tipo de Compressor
Após a avaliação do local, é hora de escolher o tipo de compressor que melhor atende às necessidades da sua operação. Existem diferentes tipos de compressores, como:
- Compressores de parafuso: São conhecidos pela eficiência energética e pela capacidade de operar de forma contínua.
- Compressores alternativos: Ideal para aplicações de baixa vazão e alta pressão.
- Compressores centrífugos: Indicados para altas vazões e são mais utilizados em grandes instalações.
A escolha do compressor deve ser baseada nas necessidades específicas da sua operação, levando em conta fatores como a pressão necessária, o volume de ar comprimido e a eficiência energética. Consultar um especialista pode facilitar essa escolha e garantir que todas as exigências de segurança e desempenho sejam atendidas.
Preparação da Instalação Elétrica
Antes da instalação do compressor, é essencial garantir que a preparação elétrica esteja em conformidade com as normas locais e os requisitos do fabricante. Isso inclui:
- Contratação de um eletricista qualificado: Profissionais capacitados sabem como preparar as ligações elétricas adequadas e garantir que as fiações e os disjuntores estejam em conformidade com os padrões de segurança.
- Adequação da fiação: A fiação deve ser dimensionada para suportar a carga elétrica do compressor, evitando sobrecargas que podem resultar em incêndios ou danos ao equipamento.
- Instalação de proteção elétrica: Dispositivos como disjuntores e relés de proteção são essenciais para garantir que ocorra a desconexão automática em casos de falhas elétricas.
Instalação e Montagem do Compressor
Com o planejamento realizado e as preparações elétricas concluídas, pode-se iniciar a instalação e montagem do compressor. Esta etapa inclui:
- Posicionamento correto: O compressor deve ser posicionado de acordo com o planejamento prévio, respeitando a área de ventilação e proporcionando acesso fácil para manutenção.
- Fixação: Dependendo do modelo, o compressor pode necessitar de suporte adicional, como bases de ancoragem, para assegurar que permaneça estável durante a operação.
- Conexões de tubulação: É fundamental conectar as tubulações de ar comprimido de maneira correta. As tubulações devem ser de material adequado, e os encaixes precisam ser estanques para evitar vazamentos.
Conexões de Segurança
As instalações de compressores industriais devem incluir conexões de segurança em conformidade com as normas. Isso envolve:
- Válvulas de alívio de pressão: Esses dispositivos são cruciais para evitar que a pressão interna do sistema alcance níveis perigosos, minimizando os riscos de explosões.
- Filtro de ar: A instalação de filtros ajuda a garantir que o ar comprimido esteja livre de contaminantes, aumentando a eficiência do sistema e prolongando a vida útil do compressor.
- Manômetros e sensores: A instalação de instrumentos de medição permite monitorar a pressão e a temperatura, garantindo que o compressor opere dentro dos limites seguros.
Testes e Ensaios
Após a conclusão da instalação, é essencial realizar testes e ensaios para garantir que tudo esteja funcionando corretamente. Essa fase inclui:
- Teste de pressão: Verifique se todos os pontos de conexão estão estanques, realizando um teste de pressão com o sistema em funcionamento.
- Verificação das conexões elétricas: A equipe deve conferir se não existem sobrecargas elétricas e se as voltagens estão dentro dos limites especificados pelo fabricante.
- Monitoramento durante o funcionamento: Observe o funcionamento do compressor durante um período de teste. Verifique se há ruídos anormais, vibrações ou qualquer tipo de falha que possa indicar um problema.
Treinamento e Capacitação dos Operadores
Uma instalação segura não se resume apenas à parte técnica. É absolutamente necessário fornecer treinamento e capacitação aos operadores que irão manusear os compressores. Esse treinamento deve abordar:
- Operação correta do equipamento: Os operadores devem entender como operar o compressor corretamente, incluindo o manuseio de controles e sistemas de segurança.
- Medidas de segurança: É importante que os trabalhadores sejam treinados em procedimentos de segurança, incluindo como agir em caso de emergência.
- Manutenção básica: Forneça instruções sobre como realizar manutenção básica, como a verificação de óleo e limpeza de filtros, para garantir que o compressor funcione corretamente ao longo do tempo.
Documentação e Conformidade com Normas de Segurança
Por último, mas não menos importante, é indispensável manter toda a documentação relacionada à instalação em ordem. Isso inclui:
- Registros de instalação: Documentar os detalhes da instalação, instruções do fabricante, garantias e faturas é crucial para futuras verificações.
- Compliance regulamentar: Verifique se a instalação atende a todas as normas e regulamentações locais de segurança e saúde ocupacional.
- Planos de manutenção: Considere criar um cronograma de manutenção preventiva que inclua inspeções e reparações regulares para maximizar a eficiência do compressor.
Conclusão
A instalação segura de compressores industriais requer atenção cuidadosa e diligente a cada uma dessas etapas. Do planejamento e avaliação do local até o treinamento dos operadores, cada fase é vital para garantir que o compressor funcione de maneira eficiente e segura. Seguir essas diretrizes não só promove a segurança, mas também melhora o desempenho geral da operação industrial.
Escolhendo o Compressor Ideal
Escolher o compressor industrial ideal é uma tarefa crítica para garantir o sucesso das operações em qualquer ambiente industrial. A escolha errada pode resultar em ineficiências operacionais, altos custos de manutenção e, no pior dos casos, interrupções no processo produtivo. Neste artigo, abordaremos os fatores fundamentais a serem considerados ao selecionar o compressor ideal para suas necessidades, incluindo tipo de compressor, requisitos de pressão e fluxo, eficiência energética, além de manutenibilidade e custo total de propriedade.
Compreendendo os Tipos de Compressores
Antes de escolher um compressor, é essencial entender os diferentes tipos disponíveis no mercado, cada um com suas próprias características e aplicações. Os principais tipos de compressores industriais incluem:
- Compressores de Parafuso: Estes compressores usam um par de parafusos rotativos para comprimir o ar. Eles são conhecidos pela sua eficiência e capacidade de operar continuamente em altas demandas. São ideais para aplicações que requerem grandes volumes de ar comprimido.
- Compressores Alternativos: Estes compressores utilizam pistões para comprimir o ar. São adequados para operações de menor capacidade e são frequentemente utilizados em situações em que a mobilidade é essencial, como em canteiros de obras.
- Compressores Centrífugos: Utilizam a força centrífuga para comprimirem o ar, sendo ideais para aplicações onde são necessários volumes altos de ar a pressões moderadas. São comumente usados em grandes fábricas e usinas.
- Compressores de Diafragma: Esses equipamentos utilizam um diafragma flexível para comprimir o ar. São a escolha ideal para aplicações que requerem ar comprimido livre de óleo, como em indústrias alimentícias e farmacêuticas.
Considerando os Requisitos de Pressão e Fluxo
Um dos fatores mais importantes ao escolher um compressor ideal é determinar os requisitos de pressão e fluxo de ar para suas operações. Isso envolve:
- Pressão de Trabalho: Determine a pressão mínima e máxima necessária para suas aplicações. O compressor deve ser capaz de fornecer essa pressão sem dificuldades. Um compressor subdimensionado pode levar a uma operação ineficiente, enquanto um superdimensionado resulta em maior consumo de energia.
- Fluxo de Ar: O fluxo de ar requerido, normalmente medido em pés cúbicos por minuto (CFM) ou litros por segundo (L/s), deve ser avaliado. Calcule o fluxo total necessário, considerando todos os equipamentos que usarão o ar comprimido.
A análise dos requisitos de pressão e fluxo permitirá que você selecione um compressor que atenda exatamente às suas necessidades sem comprometer o desempenho.
Eficiência Energética
Em um mundo onde os custos com energia estão em constante aumento, optar por um compressor eficiente em termos de energia é uma escolha inteligente. A eficiência do compressor pode impactar significativamente os custos operacionais a longo prazo. Para garantir a eficiência energética:
- Verifique o Índice de Eficiência Energética (IEE): Procure compressores com um IEE alto, que indica como o compressor converte energia elétrica em ar comprimido. Quanto mais alto o IEE, melhor será a eficiência energética do compressor.
- Avalie a Tecnologia de Compressão: Compressores modernos, como os de parafuso de velocidade variável, podem ajustar automaticamente a velocidade do motor, resultando em menor consumo de energia quando a demanda é baixa.
Tamanho e Portabilidade
O tamanho e a portabilidade do compressor são outros fatores a serem considerados, especialmente em ambientes onde o espaço é limitado. Alguns pontos a considerar incluem:
- Dimensões Físicas: Meça o espaço disponível para garantir que haja espaço suficiente para o compressor e para a circulação de ar necessário.
- Mobilidade: Se você precisará mover o compressor entre locais diferentes, considere modelos portáteis. Compressores de pequeno porte, como os alternativos, podem ser mais adequados para aplicações móveis.
Manutenibilidade e Suporte
A facilidade de manutenção também deve ser considerada ao escolher o compressor ideal. Um equipamento que requer manutenção frequente ou difícil de realizar pode levar a paradas dispendiosas. Algumas dicas para garantir a manutenibilidade incluem:
- Facilidade de Acesso: Escolha um compressor que tenha componentes acessíveis para manutenção. Isso pode facilitar a troca de peças e a realização de ajustes.
- Disponibilidade de Peças de Reposição: Verifique se as peças de reposição estão disponíveis no mercado e a rapidez com que podem ser obtidas. Isso é vital para garantir tempos de inatividade mínimos.
- Serviço e Suporte Técnico: Considere o suporte oferecido pelo fabricante. Fornecedores que oferecem assistência técnica e manutenção programada podem ser uma escolha mais segura a longo prazo.
Custos de Operação e Aquisição
Os custos iniciais de aquisição do compressor não devem ser o único critério de decisão. É fundamental avaliar o custo total de propriedade, que inclui:
- Custos de Instalação: Inclua os custos relacionados à instalação elétrica e tubulação, que podem ser significativos.
- Custos de Operação: Considere o consumo de energia, manutenção planejada e os custos com peças de reposição ao longo da vida útil do compressor.
- Custo de Paradas: Se um compressor falhar, os custos de paradas não programadas podem ser elevadíssimos. Escolher um compressor confiável pode reduzir esses custos.
Reputação do Fabricante
A reputação do fabricante é um fator importante a ser considerado ao escolher um compressor industrial. Optar por um fabricante respeitado e bem avaliado pode minimizar riscos e trazer maior segurança. Algumas coisas a considerar incluem:
- Histórico e Experiência: Verifique há quanto tempo o fabricante está no mercado e qual é sua reputação em relação à qualidade do produto e ao atendimento ao cliente.
- Testemunhos e Avaliações: Leia depoimentos de outros clientes e procure avaliações on-line sobre o desempenho dos compressores e o suporte pós-venda.
Considerações Ambientais
A escolha de um compressor também pode ter implicações ambientais. Muitos setores estão cada vez mais preocupados com a sustentabilidade. Considere as seguintes questões:
- Emissões de Carbono: Optar por compressores que utilizam tecnologias que minimizam as emissões de carbono pode ser uma escolha importante em um mundo preocupado com a mudança climática.
- Consumo de Energia: Compressores eficientes em termos energéticos não só economizam dinheiro, mas também reduzem a pegada ambiental da sua operação.
Teste e Demonstração
Antes de tomar uma decisão final, sempre que possível, solicite uma demonstração do compressor em operação. Isso lhe dará uma ideia clara do desempenho real do equipamento e permitirá que você faça perguntas sobre suas funcionalidades. Além das demonstrações, muitos fornecedores oferecem períodos de teste para que você possa avaliar o desempenho do compressor em suas operações. Esta etapa é crucial para evitar surpresas desagradáveis após a compra.
Conclusão
A escolha do compressor ideal é um processo multifacetado que envolve avaliar uma ampla gama de fatores, incluindo tipo de compressor, requisitos de pressão e fluxo, eficiência energética e custos operacionais. Ao considerar cuidadosamente cada um desses aspectos, você pode garantir que está tomando a melhor decisão para suas operações industriais, maximizando a eficiência e minimizando os custos.
Manutenção Pós-Instalação de Compressores
A manutenção pós-instalação de compressores é um aspecto fundamental para garantir a continuidade operacional, a eficiência e a durabilidade do equipamento. Um compressor bem mantido não apenas maximiza o desempenho, mas também reduz custos operacionais e o risco de paradas não programadas. Neste artigo, abordaremos as melhores práticas e procedimentos para a manutenção de compressores, incluindo inspeções regulares, troca de fluidos, monitoramento de desempenho e soluções para problemas comuns.
Importância da Manutenção Regular
A manutenção regular é vital para prolongar a vida útil do compressor e garantir seu funcionamento adequado. A falta de manutenção pode resultar em falhas mecânicas, perda de eficiência e altos custos de reparação. As principais vantagens da manutenção regular incluem:
- Redução do tempo de inatividade: Com inspeções e manutenção adequadas, a probabilidade de falhas inesperadas diminui, resultando em menos paradas para reparos.
- Eficiência energética: Compressores bem mantidos operam de forma mais eficiente, consumindo menos energia e, portanto, reduzindo os custos operacionais.
- Desempenho consistente: A manutenção assegura que o compressor funcione conforme as especificações, fornecendo um suprimento de ar comprimido confiável.
- Segurança do operador: Um compressor em boas condições é menos propenso a apresentar riscos de segurança, como vazamentos ou falhas catastróficas.
Inspeções Visuais Regulares
Realizar inspeções visuais é o primeiro passo na manutenção preventiva de compressores. Isso envolve verificar o equipamento em busca de sinais de desgaste, danos ou vazamentos. As principais áreas para inspeção incluem:
- Conexões de tubulação: Verifique se há vazamentos de ar nas conexões de tubulação, o que pode indicar a necessidade de apertar as juntas ou substituir as mangueiras.
- Fugas de óleo: Inspecione a bomba de óleo e os selos para garantir que não haja vazamentos, pois a falta de lubrificação pode causar danos sérios ao compressor.
- Componentes elétricos: Examine os cabos e conectores para evitar problemas elétricos. Fiações danificadas podem resultar em falhas elétricas.
- Filtro de ar: Verifique o filtro de ar em busca de sujeira e obstruções, o que pode afetar a eficiência do compressor.
Troca de Óleo e Filtros
A troca de óleo e de filtros é uma parte essencial da manutenção de compressores. O óleo lubrifica as peças móveis e reduz o atrito, enquanto os filtros protegem o sistema de contaminantes. A frequência da troca varia de acordo com o tipo de compressor, mas é geralmente recomendada a cada 250 a 500 horas de operação. Algumas práticas eficazes incluem:
- Escolha do Lubrificante Certo: Utilize óleo lubrificante recomendado pelo fabricante, que deve ser específico para o tipo de compressor (óleo mineral ou sintético, por exemplo).
- Verificação do Nível de Óleo: Monitore regularmente o nível de óleo e complete quando necessário. Um nível baixo de óleo pode resultar em superaquecimento e danos ao componente.
- Troca de Filtros: Substitua os filtros de ar e óleo regularmente para garantir um fluxo de ar limpo e lubrificação adequada. Filtros sujos podem causar perda de eficiência e aumento do consumo de energia.
Monitoramento de Desempenho
O monitoramento constante do desempenho do compressor pode ajudar a identificar problemas antes que eles se tornem críticos. Isso pode ser feito através de:
- Leitura de Manômetros: Observe os manômetros para garantir que a pressão de operação esteja dentro das especificações recomendadas. Pressão excessiva pode indicar um problema no sistema.
- Sensores de Temperatura: Monitore a temperatura do compressor. Se o equipamento estiver superaquecendo, isso pode sinalizar a necessidade de manutenção ou reparo.
- Sistemas de Monitoramento Inteligente: Considere a utilização de tecnologia de monitoramento remoto que permita rastrear o desempenho do compressor em tempo real. Isso facilita a identificação de anomalias rapidamente.
Limpeza Regular
A limpeza do compressor e de suas partes é fundamental para manter a eficiência e o desempenho. A sujeira e o acúmulo de detritos podem afetar a operação do equipamento. Algumas dicas incluem:
- Limpeza dos Filtros: Limpe ou substitua os filtros conforme necessário, garantindo que o fluxo de ar permaneça desobstruído.
- Remoção de Poeira: Mantenha a área ao redor do compressor livre de poeira e detritos, o que pode impedir a ventilação adequada e causar superaquecimento.
- Manutenção do Sistema de Resfriamento: Limpe as aletas de resfriamento e verifique o funcionamento dos ventiladores, se aplicável. O resfriamento adequado é essencial para evitar o superaquecimento.
Treinamento da Equipe
Uma equipe bem treinada é fundamental para garantir a manutenção adequada e a operação segura dos compressores. Realizar sessões regulares de treinamento sobre:
- Operação Segura: Certifique-se de que todos os operadores compreendam os procedimentos de operação segura, incluindo como agir em situações de emergência.
- Manutenção Básica: Treine os operadores em práticas de manutenção simples que podem ser realizadas regularmente, como troca de filtros e verificação de níveis de fluidos.
- Identificação de Problemas: Ensine a equipe a identificar sinais de problemas e a realizar auditorias visuais, reportando qualquer anomalia quanto antes.
Registro de Manutenção
Manter um registro detalhado de todas as atividades de manutenção é uma prática recomendada que pode ajudar na gestão do equipamento. Um registro adequado deve incluir:
- Data das Manutenções: Documentar cada atividade de inspeção e manutenção, indicando a data e as ações realizadas.
- Resultados de Testes: Anotar os resultados de qualquer teste realizado, como medições de pressão e temperatura.
- Observações e Recomendações: Faça anotações sobre quaisquer problemas identificados, ajustes realizados ou recomendações para ações futuras.
Planejamento de Manutenção Preventiva
A manutenção preventiva é uma prática que pode ser usada para programar atividades de manutenção regulares, antes que os problemas surgem. Um plano de manutenção preventiva deve incluir:
- Frequência de Manutenção: Defina a frequência com que os componentes críticos serão inspecionados - como semanal, mensal ou trimestral.
- Atividades Planejadas: Liste as atividades de manutenção que precisam ser realizadas em cada intervalo programado.
- Histórico de Manutenção: Ao compilar registros de manutenção, você pode ajustar e otimizar o plano ao longo do tempo de acordo com as necessidades específicas do equipamento e os resultados das manutenções anteriores.
Soluções para Problemas Comuns
Apesar de toda a manutenção, problemas podem surgir ao longo do tempo. Aqui estão algumas soluções para problemas comuns enfrentados com compressores:
- Ruído Excessivo: O aumento do ruído pode indicar problemas como componentes soltos ou desgaste. Verifique se todos os parafusos estão apertados e faça um exame detalhado do interior do compressor.
- Baixa Pressão: Se a pressão estiver abaixo do esperado, verifique se há vazamentos nas conexões ou tambores. Componentes desgastados devem ser substituídos.
- Superaquecimento: O superaquecimento pode ser causado por baixa lubrificação ou falta de ventilação. Verifique os níveis de fluido e as aberturas de ventilação para garantir que não estejam obstruídas.
Conclusão
A manutenção pós-instalação de compressores é vital para o sucesso das operações industriais. Ao seguir procedimentos de manutenção regulares, realizar inspeções visuais, trocar fluidos e filtros, monitorar o desempenho e investir na formação da equipe, você pode garantir que seus compressores operem em níveis ideais de eficiência e segurança ao longo de sua vida útil. A abordagem proativa em manutenção não só preserva o valor do ativo, mas também garante a continuidade das operações em um ambiente industrial competitivo.
Em resumo, a instalação de compressores industriais desempenha um papel fundamental no sucesso das operações de diversas indústrias. As vantagens dessa instalação vão além da eficiência operacional, abrangendo também a confiabilidade e a durabilidade do equipamento. Ao seguir as etapas necessárias para uma instalação segura e escolher o compressor ideal, as empresas podem garantir um fluxo de trabalho otimizado. Além disso, a manutenção pós-instalação é crucial para prolongar a vida útil do compressor e maximizar sua eficiência. Investir tempo e recursos nas etapas de instalação, escolha e manutenção resultará em um desempenho superior e sustentará a produtividade das operações. Portanto, esteja preparado para aplicar essas práticas e colher os benefícios de um sistema bem instalado e mantido.