Instalação de máquinas industriais para produtividade máxima
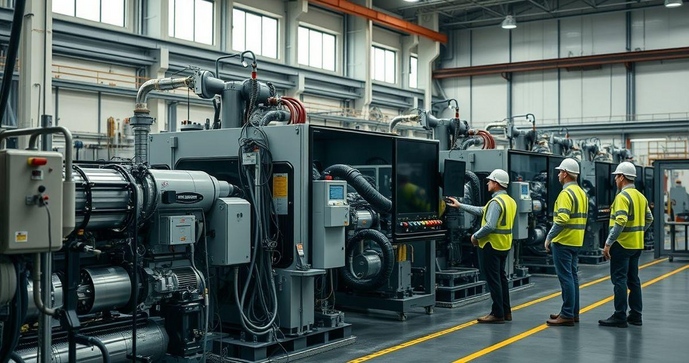
Por: Jeferson - 20 de Março de 2025
Importância do planejamento na instalação de máquinas industriais
O planejamento é uma etapa crucial no processo de instalação de máquinas industriais, pois influencia diretamente na eficiência e segurança das operações. Um planejamento meticuloso permite identificar as necessidades específicas da empresa, avaliar os recursos disponíveis e alinhar as expectativas com a realidade operacional.
Primeiramente, um bom planejamento começa com a análise detalhada do espaço onde as máquinas serão instaladas. Isso inclui a avaliação das dimensões do local, acessibilidade e infraestrutura elétrica necessária para suportar o funcionamento dos equipamentos. Uma má escolha do local pode resultar em dificuldades operacionais e comprometimento da segurança.
Além disso, o planejamento deve incluir uma análise dos processos produtivos existentes. Compreender como as novas máquinas se integrarão a esses processos ajudará a otimizar a produção e minimizar interrupções. A integração harmoniosa é essencial para baixar custos e aumentar a produtividade.
Outro aspecto a se considerar é o cronograma de instalação. É fundamental estabelecer um timeline realista que não interfira na operação da fábrica. Planejar dentro do tempo ideal é vital para evitar paralisações e manter o fluxo de trabalho. Um cronograma bem elaborado permite que a equipe se prepare adequadamente para os novos desafios e mudanças.
Ademais, o planejamento deve incluir uma estratégia de comunicação. Envolver toda a equipe no processo é essencial para garantir que todos estejam cientes das mudanças e suas funcionalidades. A comunicação eficaz ajuda a minimizar erros durante a instalação e assegura que todos estejam alinhados com os objetivos esperados.
Por fim, uma avaliação dos fornecedores de máquinas é igualmente importante. Escolher fornecedores confiáveis que ofereçam suporte técnico e garantia adequada é um ponto vital. Isso assegura que qualquer eventualidade durante o processo de instalação será tratada rapidamente, reduzindo o tempo de inatividade e aumentando a confiabilidade do sistema produtivo.
Em resumo, o planejamento é fundamental para uma instalação bem-sucedida de máquinas industriais. Ao considerar todos os aspectos mencionados, as empresas podem garantir que a implantação ocorra de forma eficiente, contribuindo para a otimização dos processos e para o sucesso do negócio.
Passos essenciais para uma instalação segura e eficiente
A instalação de máquinas industriais requer atenção a vários detalhes para garantir não apenas a eficiência, mas também a segurança de todos os colaboradores envolvidos. Seguir passos essenciais pode facilitar esse processo e minimizar riscos. Aqui estão os passos fundamentais para uma instalação segura e eficiente:
1. Revisão da documentação técnica: Antes de iniciar a instalação, é fundamental revisar toda a documentação técnica fornecida pelo fabricante. Isso inclui manuais de instalação, especificações de segurança e recomendações de operação. Essa revisão ajuda a compreender melhor as necessidades específicas das máquinas e orientações para uma instalação adequada.
2. Formação da equipe: Os profissionais envolvidos na instalação devem ser adequadamente treinados e capacitados. Realizar reuniões prévias para discutir o procedimento e esclarecer dúvidas é crucial. É aconselhável que uma equipe experiente ou um técnico autorizado do fabricante esteja presente para orientar o processo.
3. Preparação do local: Antes da chegada das máquinas, o local deve ser preparado. Isso inclui a realização de ajustes estruturais, verificação da infraestrutura elétrica e garantia de que o espaço atende às exigências de segurança, como a presença de extintores e sinalizações adequadas.
4. Equipamentos de proteção individual (EPIs): O uso de EPIs adequados deve ser uma prioridade. equipamentos como capacetes, luvas, protetores auriculares e óculos de segurança devem ser fornecidos aos trabalhadores envolvidos na instalação. Esses itens ajudam a prevenir acidentes e garantir a segurança no ambiente de trabalho.
5. Montagem e alinhamento corretos: A montagem das máquinas deve ser realizada com cautela, seguindo as instruções do fabricante rigorosamente. Um alinhamento incorreto pode resultar em falhas operacionais e desgaste precoce dos equipamentos. Certifique-se de que todas as peças estejam firmemente fixadas e que os componentes estejam alinhados conforme descrito no manual.
6. Testes e validações: Após a instalação, é essencial realizar testes de funcionamento das máquinas. Esses testes devem incluir a verificação de todos os sistemas, como ações de segurança, ajustes de velocidade e controle de cargas. Validar o funcionamento completo antes de iniciar a produção evita problemas futuros e assegura que tudo esteja operando de forma correta.
7. Documentação do processo: Registrar todas as etapas da instalação, incluindo eventuais ajustes e problemas encontrados, é uma prática recomendada. Essa documentação serve como um relatório para futuras referências e facilita intervenções necessárias ao longo do ciclo de vida da máquina.
Seguir esses passos essenciais é fundamental para garantir uma instalação segura e eficiente de máquinas industriais. Ao incorporar estas práticas, as empresas podem otimizar seus processos e assegurar um ambiente de trabalho seguro para todos os colaboradores.
Equipamentos de proteção obrigatórios durante a instalação
A instalação de máquinas industriais envolve diversos riscos e, por isso, a utilização de equipamentos de proteção individual (EPIs) é fundamental para garantir a segurança dos trabalhadores. Abaixo, estão os principais equipamentos de proteção obrigatórios que devem ser utilizados durante esse processo:
1. Capacete de segurança: O capacete é essencial para proteger a cabeça contra impactos e quedas de objetos. É fundamental utilizar um capacete que atenda às normas de segurança. Não deve ser utilizado um capacete danificado ou com partes faltando.
2. Óculos de proteção: Os óculos de proteção são indispensáveis para evitar lesões nos olhos, principalmente em ambientes onde há risco de projeção de partículas. É importante que os óculos sejam de um modelo que não embarace e que se ajuste confortavelmente no rosto.
3. Protetores auriculares: Durante a instalação, é possível que os trabalhadores estejam expostos a níveis elevados de ruído. O uso de protetores auriculares ajuda a prevenir danos auditivos e a garantir a concentração durante a execução das tarefas.
4. Luvas de proteção: As luvas são necessárias para proteger as mãos contra cortes, arranhões e produtos químicos. Diferentes tipos de luvas podem ser utilizadas, dependendo da natureza do trabalho, como luvas de borracha, couro ou materiais resistentes a cortes.
5. Botas de segurança: O uso de botas de segurança com biqueiras reforçadas é fundamental para proteger os pés contra quedas de objetos pesados. As botas devem ter solado antiderrapante para evitar escorregões em superfícies molhadas ou oleosas.
6. Máscaras de proteção: Quando a instalação envolve trabalho com produtos químicos, poeiras ou vapores, é crucial o uso de máscaras de proteção respiratória. Elas ajudam a prevenir problemas respiratórios causados por inalação de substâncias nocivas.
7. Equipamentos de proteção adicional: Dependendo das especificidades da instalação, pode ser necessário utilizar equipamentos adicionais, como cintos de segurança para trabalhos em altura ou ventiladores para áreas com pouca circulação de ar.
O uso adequado desses EPIs não apenas protege os trabalhadores, mas também contribui para um ambiente de trabalho mais seguro e eficiente. Ao final da instalação, é necessário que todos os equipamentos sejam inspecionados e higienizados para estar prontos para um novo uso. Priorizar a segurança deve ser um dos principais objetivos em qualquer projeto de instalação de máquinas industriais.
Integração de máquinas com sistemas já existentes
A integração de novas máquinas industriais com sistemas já existentes é um passo crítico para otimizar a operação e maximizar a eficiência produtiva. Essa interconexão pode trazer diversos benefícios, mas também apresenta desafios que precisam ser abordados cuidadosamente.
A seguir, discutiremos as principais considerações e etapas para assegurar uma integração bem-sucedida:
1. Avaliação das necessidades de integração: Antes de tudo, é essencial realizar uma avaliação das necessidades e expectativas da empresa. Isso envolve identificar quais processos precisam ser integrados, que tipo de dados precisam ser trocados entre as máquinas e como a nova instalação pode melhorar a eficiência das operações em andamento.
2. Análise da compatibilidade: Um fator chave na integração é a compatibilidade entre as novas máquinas e os sistemas existentes. É fundamental verificar se as tecnologias utilizadas nas máquinas são compatíveis com os sistemas de automação, controle e monitoramento já implementados na fábrica. Isso pode incluir a verificação de protocolos de comunicação e interfaces compatíveis.
3. Planejamento da interface de comunicação: A criação de uma interface de comunicação clara entre as máquinas é essencial para garantir que possam operar em harmonia. O desenvolvimento de protocolos para a troca de dados e informações, como o uso de redes industriais, é imprescindível. Além disso, utilizar sistemas baseados em IoT (Internet das Coisas) pode facilitar essa comunicação ao tornar os dispositivos mais interconectados.
4. Testes e validações: Após a integração das máquinas, é crucial executar um conjunto de testes para assegurar que todos os sistemas funcionem conforme o esperado. Esses testes devem incluir verificação de funcionalidades, alinhamento de dados e monitoramento de performance para garantir que a nova configuração atenda às expectativas da empresa. A realização de testes em ambientes controlados pode ajudar a identificar problemas antes que sejam gerados na operação real.
5. Treinamento da equipe: A equipe operacional deve ser capacitada para utilizar os novos sistemas integrados. Treinamentos específicos devem ser realizados para familiarizá-los com as funcionalidades das novas máquinas e como interagir eficientemente com os sistemas existentes. Essa formação é vital para garantir uma transição suave e minimizar interrupções.
6. Monitoramento contínuo: Após a integração, é fundamental estabelecer um programa de monitoramento contínuo para avaliar a eficiência do sistema integrado. Isso inclui a coleta de dados sobre o desempenho das máquinas e a análise de indicadores-chave de desempenho (KPIs) para identificar áreas que possam requerer ajustes ou melhorias. Essa abordagem proativa pode ajudar a detectar problemas antes que afetem a produção.
A integração bem-sucedida de máquinas novas com sistemas já existentes pode resultar em melhorias significativas na eficiência operacional e na produtividade. A abordagem estruturada e a atenção aos detalhes são fundamentais para compensar os desafios que podem surgir durante o processo. Quando realizada corretamente, a integração se torna uma peça-chave para o sucesso no ambiente industrial atual.
Manutenção preventiva após a instalação das máquinas
A manutenção preventiva após a instalação das máquinas é uma prática essencial para assegurar o funcionamento contínuo e eficiente dos equipamentos industriais. Essa abordagem ajuda a minimizar falhas, prolongar a vida útil das máquinas e garantir a segurança no ambiente de trabalho.
1. Estabelecimento de um plano de manutenção: É crucial desenvolver um plano de manutenção detalhado que inclua inspeções regulares, lubrificações, ajustes e substituições de peças, conforme as recomendações do fabricante. Esse plano deve ser adaptado às necessidades específicas de cada máquina e ao volume de operação.
2. Treinamento da equipe: A equipe responsável pela manutenção deve ser devidamente treinada e capacitada para realizar inspeções e reparos nas máquinas. O conhecimento técnico adequado é fundamental para identificar problemas precoces e realizar intervenções rápidas, evitando paradas inesperadas.
3. Inspeções regulares: As inspeções devem ser agendadas de forma periódica para verificar o estado das máquinas, identificar desgastes, vazamentos e sinais de falha. Esses check-ups são essenciais para garantir que todos os componentes estejam operando corretamente e que possíveis problemas sejam solucionados antes que se tornem graves.
4. Documentação das manutenções: Registrar todas as atividades de manutenção realizadas é fundamental. Isso inclui detalhes sobre as inspeções, serviços executados, peças trocadas e quaisquer anotações sobre o desempenho das máquinas. A documentação é útil não apenas para fins de rastreamento histórico, mas também para referência futura em caso de falhas recorrentes.
5. Análise de desempenho: Monitorar o desempenho das máquinas é uma parte crucial da manutenção preventiva. Isso envolve analisar dados operacionais, como eficiência e produtividade, para identificar possíveis áreas de melhoria. A análise constante ajuda a antecipar a necessidade de serviços adicionais e ajustes, otimizando os processos industriais.
6. Substituição programada de peças: Algumas peças têm uma vida útil específica e devem ser substituídas regularmente para evitar falhas. A manutenção preventiva deve incluir a identificação de componentes críticos e a programação de suas trocas em intervalos recomendados, como correias, filtros, e rolamentos.
7. Revisão do ambiente operacional: O ambiente onde as máquinas estão instaladas pode impactar seu desempenho. Manter as áreas de operação limpas, livres de obstruções e com boa ventilação é essencial para otimizar a eficiência e a segurança. A avaliação constante do ambiente operacional pode prevenir problemas que afetam a performance dos equipamentos.
A manutenção preventiva, quando realizada de forma consistente e metódica, é vital para garantir que as máquinas operem de maneira segura e eficiente ao longo do tempo. Investir nessa prática não apenas protege o capital investido, mas também assegura a continuidade da produção e a segurança dos colaboradores.
Capacitação da equipe para operar novas máquinas industriais
A capacitação da equipe para operar novas máquinas industriais é um aspecto crítico que pode determinar o sucesso da implementação e operação eficaz dos equipamentos. A formação adequada não apenas facilita a adaptação às novas tecnologias, mas também minimiza riscos e aumenta a produtividade.
A seguir, exploramos os principais elementos envolvidos no processo de capacitação:
1. Análise das necessidades de treinamento: Antes de iniciar a capacitação, é vital realizar uma análise das necessidades de treinamento com base nas habilidades atuais da equipe e nas exigências específicas das novas máquinas. Esta avaliação ajuda a identificar lacunas de conhecimento e as áreas que necessitam de foco durante o treinamento.
2. Desenvolvimento de um programa de treinamento: Após identificar as necessidades, um programa de treinamento estruturado deve ser elaborado. Esse programa deve incluir o conhecimento teórico sobre o funcionamento das máquinas, bem como práticas operacionais. Incluir módulos sobre segurança e manutenções básicas também é essencial para garantir que todos os aspectos operacionais sejam cobertos.
3. Utilização de diferentes métodos de ensino: A combinação de diferentes métodos de ensino – como aulas teóricas, workshops práticos, vídeos instrutivos e demonstrações ao vivo – pode enriquecer a experiência de aprendizado. Essa abordagem permite que os operadores se familiarizem com os equipamentos de diversas maneiras, aumentando a retenção de conhecimento.
4. Envolvimento de especialistas: Convidar especialistas, como técnicos de fábrica ou representantes do fabricante, para ministrar o treinamento pode proporcionar insights valiosos. Esses profissionais possuem conhecimento aprofundado sobre as máquinas e podem compartilhar dicas e soluções práticas que beneficiam a equipe.
5. Treinamento contínuo: A capacitação não deve ser um evento único, mas um processo contínuo. A realização de treinamentos regulares e atualizações quanto a novas funcionalidades ou melhorias de equipamentos garante que a equipe permaneça informada e preparada para lidar com quaisquer desafios que possam surgir ao longo do tempo.
6. Avaliação do aprendizado: Para garantir que o treinamento foi eficaz, é importante implementar avaliações que testem o aprendizado da equipe. Essas avaliações podem incluir testes práticos e teóricos, além de feedback das atividades em campo que ajudem a identificar áreas que ainda precisam de atenção.
7. Incentivar um ambiente de aprendizado: Criar uma cultura de segurança e aprendizado dentro da empresa é fundamental. Incentivar os membros da equipe a compartilhar experiências e desafios enfrentados, bem como promover a troca de conhecimentos, fortalece a equipe e inclui todos no processo de aprendizagem.
A capacitação adequada da equipe para operar novas máquinas é essencial para maximizar a eficiência e a segurança no ambiente industrial. Ao investir no treinamento, as empresas podem garantir não apenas a adaptação aos novos equipamentos, mas também um ambiente de trabalho mais seguro e produtivo.
Em suma, a instalação e operação de máquinas industriais envolvem uma série de etapas fundamentais, desde o planejamento inicial até a capacitação da equipe.
Priorizar a segurança, a eficiência e a manutenção preventiva são ações cruciais que garantem a longevidade dos equipamentos e a otimização dos processos produtivos.
A integração das máquinas com sistemas existentes e a implementação de treinamentos contínuos para a equipe também contribuem significativamente para a melhoria da produtividade e para um ambiente de trabalho seguro.
Ao investir tempo e recursos adequados em cada uma dessas etapas, as empresas podem alcançar resultados significativos, impulsionando seu crescimento e competitividade no mercado.