Manutenção Industrial: Melhore sua Produtividade
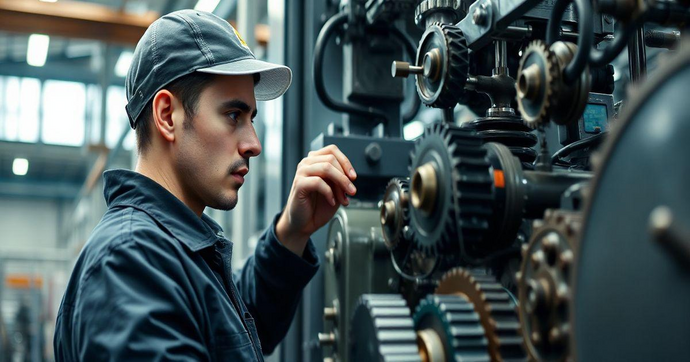
Por: Jeferson - 24 de Dezembro de 2024
Manutenção Industrial é um fator-chave para garantir a eficiência e a longevidade dos equipamentos em uma organização. Neste artigo, abordaremos as diferentes abordagens de manutenção e sua importância para otimizar processos produtivos. Você descobrirá como práticas eficazes podem reduzir falhas, aumentar a produtividade e, consequentemente, promover uma economia significativa. Continue lendo para aprender como implementar estratégias eficazes de manutenção em sua empresa.
Importância da Manutenção Industrial
A Manutenção Industrial desempenha um papel vital no funcionamento eficaz de qualquer empresa que depende de maquinários e equipamentos. Suas principais funções vão além de evitar falhas; ela garante a continuidade da produção, proporciona segurança aos colaboradores e pode impactar diretamente na eficiência operacional. Neste sentido, entender a importância da manutenção pode ser o diferencial entre o sucesso e o fracasso de um negócio.
Um dos principais benefícios da manutenção industrial é a redução de custos. Equipamentos que não recebem cuidados regulares são propensos a falhas que podem resultar em paradas não programadas. Essas paradas interrompem a produção, gerando atrasos e aumentando os custos operacionais. Com uma programação de manutenção adequada, é possível evitar surpresas desagradáveis e garantir que os equipamentos estejam sempre operando em sua capacidade máxima.
A manutenção não se limita apenas à manutenção corretiva, mas abrange também a manutenção preventiva e preditiva. A manutenção preventiva, por exemplo, é realizada em intervalos regulares com o objetivo de evitar falhas futuras. Já a manutenção preditiva utiliza tecnologias avançadas, como sensores e análises de dados, para prever quando determinado equipamento pode falhar, permitindo que a equipe técnica intervenha antes que um problema aconteça.
Além dos benefícios econômicos, a manutenção industrial exerce um papel crucial na segurança do trabalho. Equipamentos mal mantidos podem representar riscos sérios à saúde e segurança dos colaboradores. Funcionários que operam máquinas com falhas podem se machucar ou causar acidentes graves. Portanto, investir em uma boa estratégia de manutenção não só protege o patrimônio da empresa, mas também garante que seus colaboradores estejam seguros enquanto executam suas funções.
Outro ponto importante é a conformidade com normas regulatórias e padrões de segurança do setor. Muitas indústrias estão sujeitas a regulamentações rigorosas que exigem que o equipamento esteja em conformidade com certos padrões. A manutenção regular ajuda a garantir que a empresa esteja em conformidade, evitando multas e sanções que podem surgir de inspeções inadequadas. Isso é especialmente relevante para indústrias que operam em setores críticos, como alimentação, farmacêutico e automobilístico, onde a segurança e a qualidade são primordiais.
Corrigir problemas de forma proativa também contribui para a construção de um ambiente de trabalho positivo. Quando os colaboradores percebem que a empresa investe em manutenção e segurança, isso aumenta a moral da equipe. Um ambiente onde os funcionários se sentem seguros e valorizados resulta em maior produtividade e engajamento. Assim, as empresas que priorizam a manutenção industrial não só cuidam de seus ativos, mas também promovem um clima organizacional favorável.
A utilização de tecnologia e inovação na manutenção industrial é uma tendência crescente. A digitalização e o uso de inteligência artificial ajudam a otimizar processos e melhorar a eficácia da manutenção. A análise de dados permite que as equipes identifiquem padrões e estabeleçam rotinas de manutenção mais eficientes. O uso de software de gestão de manutenção pode simplificar a programação e o rastreamento das atividades, tornando o processo ainda mais eficiente.
Investir em manutenção industrial também é essencial para prolongar a vida útil dos equipamentos. Com a devida atenção e cuidados, maquinários e equipamentos podem durar muito mais do que o previsto. Isso significa um melhor retorno sobre o investimento feito em maquinário e menos necessidade de compras frequentes de novos equipamentos. Além disso, a valorização do ativo pode ser um dos fatores que fortalece a posição da empresa no mercado.
Por fim, ao focar na importância da manutenção industrial, as empresas podem melhorar sua imagem no mercado e construir a confiança entre clientes e parceiros. Equipamentos em boas condições e processos eficientes refletem a seriedade e o compromisso da empresa com a qualidade. Isso pode ser um diferencial competitivo em um mercado cada vez mais exigente.
Concluindo, a manutenção industrial é um elemento fundamental que não deve ser negligenciado. Com custos reduzidos, segurança garantida, conformidade regulatória, ambiente de trabalho positivo, utilização de tecnologia e valorização de ativos, torna-se clara a importância de implementar uma cultura de manutenção eficaz dentro das organizações. Para empresas que buscam uma solução adicional, a Instalação de alambrados pode ser uma boa opção para manter a segurança nas instalações, complementando assim os esforços em manter os maquinários e a equipe em pleno funcionamento. A abordagem proativa direcionada à manutenção é a chave para o sucesso industrial.
Tipos de Manutenção Industrial
Quando falamos em Manutenção Industrial, é fundamental entender os diversos tipos que existem, pois cada modalidade tem suas características e adequações específicas. As empresas precisam escolher a abordagem mais apropriada conforme seus objetivos, orçamento e condições operacionais. Neste artigo, abordaremos os principais tipos de manutenção industrial, destacando suas vantagens e desvantagens.
O primeiro tipo a ser mencionado é a manutenção corretiva. Esse tipo de manutenção ocorre após a falha do equipamento, com o objetivo de restaurá-lo a um estado operacional adequado. Muitos negócios adotam essa abordagem inicialmente devido à sua aparente simplicidade e baixos custos de implementação. No entanto, a manutenção corretiva pode resultar em paradas inesperadas, comprometendo a produção e acarretando custos adicionais. Portanto, é importante avaliar se essa abordagem vale a pena, especialmente em ambientes de alta demanda.
A manutenção preventiva é outro tipo amplamente adotado nas indústrias. Essa abordagem envolve a realização de inspeções e serviços programados em intervalos regulares, independentemente do estado do equipamento. O principal objetivo é evitar falhas antes que elas ocorram, garantindo que a operação continue sem interrupções. As vantagens da manutenção preventiva incluem a prolongação da vida útil dos equipamentos e a redução do número de falhas inesperadas, resultando em uma operação mais eficiente. Contudo, essa abordagem pode exigir um investimento anualmente, o que pode ser um desafio para pequenas empresas.
A manutenção preditiva é uma evolução da manutenção preventiva. Ela utiliza tecnologias avançadas, como sensores, termografia e análise de vibrações, para monitorar continuamente o estado dos equipamentos. A ideia é prever quando uma falha pode ocorrer, permitindo intervenções antes que o problema aconteça. Assim, os custos com manutenção são reduzidos, pois as intervenções são feitas apenas quando necessário. No entanto, a implementação de manutenção preditiva requer investimentos em tecnologia e treinamento dos colaboradores para que saibam interpretar os dados coletados.
Outro tipo importante é a manutenção detectiva, que se concentra na realização de testes e medições para identificar quaisquer anomalias antes que um problema se concretize. Esse tipo de manutenção é essencial nas indústrias onde a segurança é uma prioridade, como na área química e petroquímica. A manutenção detectiva combina técnicas de monitoramento com testes regulares, garantindo que os equipamentos estejam seguros e operando dentro de parâmetros aceitáveis.
Além desses, existe a manutenção de melhoria, que se dedica a aprimorar equipamentos e processos existentes. Esse tipo de manutenção visa não apenas garantir que os equipamentos funcionem, mas também melhorar seu desempenho e eficiência. Isso pode incluir atualizações tecnológicas, otimizações de processo ou até mesmo modificações estruturais. A manutenção de melhoria é especialmente importante em indústrias competitivas, onde a inovação pode ser um diferencial significativo.
Nos últimos anos, a manutenção baseada em condição tem ganhado espaço. Essa modalidade considera o estado real do equipamento em um determinado momento, decisão que é influenciada por indicadores como temperatura, vibração e desgaste. Ao coletar e analisar esses dados, as equipes podem determinar o momento mais adequado para realizar a manutenção. Esse modelo tem se mostrado eficiente, pois permite intervenções mais eficientes, economizando tempo e recursos. Assim como a manutenção preditiva, a manutenção baseada em condição também exige investimento em tecnologia.
A escolha entre os tipos de manutenção industrial deve ser avaliada de acordo com as especificidades e estratégias de cada negócio. Optar por uma estratégia híbrida, que combine diferentes tipos de manutenção, pode ser a solução ideal para maximizar a eficiência e minimizar custos. Muitas empresas se beneficiam de uma mistura de manutenção preventiva, preditiva e corretiva, permitindo que desenvolvam um plano de manutenção abrangente.
Finalmente, é essencial que as empresas envolvam suas equipes de trabalho nesse processo. Treinamento e capacitação são fundamentais para que os colaboradores entendam as estratégias de manutenção em uso e possam colaborar para sua implementação bem-sucedida. Além disso, um Empresa de mecânica industrial pode complementar esses esforços, proporcionando o suporte técnico necessário ao desenvolvimento de um plano de manutenção eficiente.
Em suma, conhecer os diferentes tipos de manutenção industrial é imprescindível para as empresas que buscam aumentar a eficiência e reduzir custos. Cada uma das abordagens tem suas características, vantagens e desvantagens, que devem ser cuidadosamente consideradas na hora de elaborar um plano de manutenção bem-sucedido. Um gerenciamento eficaz da manutenção pode trazer benefícios significativos, tornando a operação mais confiável e produtiva.
Benefícios da Manutenção Preventiva
A manutenção preventiva tem se mostrado uma prática essencial nas indústrias modernas, oferecendo uma série de benefícios que comprometem diretamente a eficiência operacional e a lucratividade das empresas. Ao contrário da manutenção corretiva, que é realizada apenas quando um equipamento falha, a manutenção preventiva ocorre de forma programada e sistemática, com o objetivo de evitar esse tipo de falha. Neste artigo, vamos explorar os principais benefícios da manutenção preventiva e como ela pode impactar positivamente o desempenho industrial.
Um dos principais benefícios da manutenção preventiva é a redução de custos. Embora possa parecer que invertir recursos em manutenção programada é um gasto desnecessário, na verdade, trata-se de um investimento que reduz os custos com reparos emergenciais e paradas inesperadas. Equipamentos que não recebem a devida manutenção tendem a apresentar falhas com maior frequência, resultando em despesas significativas com consertos, além de impactar negativamente a produção. Com a manutenção preventiva, a empresa pode evitar essas situações, garantindo um funcionamento contínuo e mais eficiente de suas operações.
Outro benefício relevante é a aumento da vida útil dos equipamentos. Ao realizar inspeções e manutenções rotineiras, as empresas conseguem identificar desgastes e problemas técnicos antes que se tornem sérios, permitindo que as peças sejam reparadas ou substituídas no momento adequado. Isso não só prolonga a vida útil do maquinário como também evita investimentos frequentes na compra de novos equipamentos. A disponibilidade de recursos financeiros pode ser melhor utilizada, reforçando o crescimento da empresa em outras áreas.
A segurança no ambiente de trabalho é outro fator crucial que se beneficia da manutenção preventiva. Equipamentos mal conservados podem representar riscos significativos para os colaboradores, levando a acidentes de trabalho. A manutenção preventiva assegura que os dispositivos de segurança estejam funcionando corretamente, reduzindo assim a probabilidade de acidentes. Além disso, a implementação de protocolos de manutenção demonstra o comprometimento da empresa com a segurança de seus funcionários, o que pode aumentar a moral e o engajamento da equipe.
A manutenção preventiva também contribui para a melhora na qualidade do produto. Com máquinas funcionando de forma otimizada e sem interrupções, a produção tende a ser mais consistente e livre de falhas. Isso se traduz em produtos finais de maior qualidade, o que pode resultar em maior satisfação do cliente e uma reputação positiva para a empresa no mercado. Quando os produtos atendem às expectativas, aumenta a confiança dos consumidores e as chances de fidelização.
Outro ponto importante é o planejamento operacional. A manutenção preventiva permite que as empresas tenham um controle mais eficiente sobre suas operações. Ao planejar as manutenções de forma proativa, é possível programar paradas que permitam a execução de tarefas sem impactar o fluxo de trabalho. Dessa forma, as interrupções podem ser minimizadas e as atividades de produção podem ser conduzidas de maneira mais organizada. Uma abordagem estruturada para a manutenção traz mais previsibilidade e reduz a incerteza, aspectos fundamentais para o planejamento estratégico da companhia.
Além disso, a manutenção preventiva permite a integração de novas tecnologias. Hoje em dia, muitas empresas utilizam softwares e sistemas de monitoramento para programar manutenções e acompanhar o desempenho de seus equipamentos. Ao optar pela manutenção preventiva, as empresas podem implementar esses sistemas de forma mais eficiente, coletando dados que ajudem na tomada de decisões. A análise de dados facilita a identificação de tendências e a adoção de melhorias contínuas, elementos essenciais para a competitividade em um mercado dinâmico.
A redução de impactos ambientais também é um benefício significativo da manutenção preventiva. Equipamentos mal conservados podem causar vazamentos e emissões maiores do que o permitido, comprometendo normas ambientais e a imagem da empresa. Com a manutenção regular, as empresas garantem que seus equipamentos operem dentro dos padrões adequados, minimizando impactos negativos no meio ambiente. Essa conscientização ambiental pode se tornar um diferencial competitivo para as organizações, que são cada vez mais cobradas por práticas sustentáveis.
Por fim, empresas que se destacam em manutenção preventiva podem criar uma base sólida para discussões futuras sobre otimização e inovação. A boa gestão da manutenção proporciona um ambiente favorável para explorar melhorias tecnológicas e processos inovadores. Entre as Empresas de pintura industrial , muitas estão aderindo a práticas de manutenção que permitem não apenas a preservação de ativos, mas também a busca constante por inovações que podem otimizar ainda mais seus processos.
Em resumo, os benefícios da manutenção preventiva se estendem por diversos aspectos operacionais e estratégicos das empresas. Desde a redução de custos até o aumento da segurança, essa prática se demonstra cada vez mais essencial para o sucesso e a sustentabilidade dos negócios. As organizações que investirem em estratégias de manutenção preventiva estarão, com certeza, à frente de seus concorrentes, garantindo uma operação mais eficiente, segura e rentável.
Sistemas de Gestão de Manutenção
No ambiente industrial atual, a eficiência operacional é uma prioridade, e para isso, as empresas necessitam de ferramentas que facilitem a administração de seus ativos. Os Sistemas de Gestão de Manutenção (SGM) surgem como soluções essenciais para otimizar a manutenção de equipamentos e infraestrutura. Estes sistemas auxiliam as organizações a planejar, monitorar e executar suas atividades de manutenção de forma eficaz, resultando em diversos benefícios. Neste artigo, exploraremos os principais aspectos dos Sistemas de Gestão de Manutenção e como eles podem impactar a operação de uma empresa.
Um Sistema de Gestão de Manutenção é um conjunto de processos e ferramentas que integram a gestão de ativos, visando garantir a eficiência, a segurança e a disponibilidade dos equipamentos. Esses sistemas podem ser baseados em software ou podem englobar processos manuais, garantindo que todas as informações sejam capturadas e analisadas. A escolha de um SGM apropriado pode ser um divisor de águas para empresas que buscam otimizar seus processos e reduzir custos operacionais.
Um dos principais benefícios de um SGM é a organização dos dados de manutenção. Muitas vezes, as informações sobre manutenções passadas e programadas ficam dispersas em planilhas ou documentos físicos, o que pode criar dificuldades na recuperação de informações e no planejamento de novas intervenções. Com um SGM, todas essas informações são centralizadas, facilitando a consulta e análise de dados. A partir daí, é possível verificar quais equipamentos necessitam de mais atenção e quais estratégias de manutenção têm se mostrado mais eficazes ao longo do tempo.
Além disso, os Sistemas de Gestão de Manutenção promovem a programação e agendamento de manutenções. Ao utilizar um software adequado, os gestores podem planejar facilmente as atividades de manutenção preventiva e corretiva, evitando paradas indesejadas e otimizando a utilização do tempo dos colaboradores. Isso é especialmente importante em ambientes industriais onde o tempo de inatividade pode resultar em grandes perdas financeiras. A programação eficiente também garante que os recursos necessários, como peças de reposição e mão de obra, estejam disponíveis quando necessário.
Outro fator crucial é a melhoria na comunicação entre as equipes. Sistemas de Gestão de Manutenção facilitam a troca de informações entre as equipes de manutenção e operação. Por meio de um sistema centralizado, todos os colaboradores têm acesso às mesmas informações, o que reduz a possibilidade de erros e mal-entendidos. Além disso, notificar a equipe sobre manutenções programadas ou emergenciais se torna mais fácil, permitindo uma coordenação eficiente e o alinhamento das atividades.
A redução de custos também é uma consequência positiva da implementação de um SGM. Através do monitoramento contínuo e da análise de dados, as empresas podem identificar equipamentos que apresentam frequente necessidade de manutenção, permitindo a tomada de decisões informadas sobre a vida útil dos ativos. Isso pode levar a uma redução significativa nos custos operacionais e na necessidade de reparos dispendiosos. O gerenciamento eficiente das manutenções resulta em uma operação mais econômica e sustentável.
Além disso, um SGM oferece à empresa um monitoramento em tempo real dos ativos e desempenho das máquinas. Muitos sistemas modernos contam com a integração de tecnologias como Internet das Coisas (IoT), permitindo a coleta de dados em tempo real. Com essa informação à disposição, as empresas podem identificar problemas antes que se agravem, realizando manutenções proativas e evitando paradas indesejadas. Esse tipo de abordagem é especialmente útil em ambientes de produção industrial, onde a continuidade das operações é fundamental.
Os Sistemas de Gestão de Manutenção também são ferramentas valiosas para a geração de relatórios e análise de desempenho. Com a automação de processos, é possível gerar relatórios detalhados sobre a eficácia das manutenções, a frequência de falhas e a utilização dos ativos. Esses dados possibilitam que os gestores identifiquem tendências e padrões que podem ser utilizados para aprimorar as estratégias de manutenção e a tomada de decisões empresariais a longo prazo. Assim, as empresas conseguem realizar um mapeamento de suas operações e работают continuamente para a excelência.
Outro aspecto que não pode ser negligenciado é o treinamento e capacitação da equipe. A implementação de um Sistema de Gestão de Manutenção geralmente requer que os colaboradores sejam treinados para usar a nova plataforma. Isso não apenas melhora a adesão ao sistema, mas também cria uma cultura de responsabilidade em relação à manutenção, onde todos na empresa entendem a importância desses processos para o sucesso do negócio.
Além disso, à medida que as empresas crescem e suas operações se tornam mais complexas, ter um sistema robusto para gerenciar a manutenção torna-se crítico. Um SGM bem estruturado pode escalar com a empresa, adaptando-se às novas necessidades e demandas que surgem ao longo do tempo. A flexibilidade dos sistemas permite que as empresas continuem a otimizar suas operações em um mercado em constante evolução.
Por último, mas não menos importante, o investimento em um Sistema de Gestão de Manutenção pode refletir positivamente na imagem da empresa. A reputação de uma organização é fundamental no mercado atual e ter um sistema que assegure a eficiência operacional e a segurança pode ser um diferencial significativo. Isso demonstra comprometimento com a qualidade, segurança e, consequentemente, com a satisfação do cliente.
Portanto, considerar a implementação de um Sistema de Gestão de Manutenção é um passo fundamental para qualquer empresa que busca otimizar suas operações e garantir a eficiência dos seus ativos. As empresas que abraçam essas tecnologias não apenas estão se preparando para os desafios de hoje, mas também estão se posicionando para um futuro mais eficiente e sustentável. A integração com outros processos, como a manutenção do Piso gail industrial , pode fornecer ainda mais vantagens competitivas, contribuindo para um gerenciamento holístico e eficaz das operações industriais.
Técnicas para Planejamento de Manutenção
O planejamento de manutenção é um aspecto crucial para garantir a eficiência operacional nas empresas, especialmente em ambientes industriais onde os ativos são vitais para a produção. A aplicação de técnicas adequadas de planejamento pode ajudar a minimizar custos, aumentar a segurança e melhorar a produtividade. Neste artigo, exploraremos algumas das principais técnicas utilizadas para o planejamento de manutenção, permitindo que as empresas desenvolvam uma estratégia eficaz e eficiente.
Uma das técnicas mais utilizadas no planejamento de manutenção é o método de manutenção baseada em condição. Este método envolve a monitoração contínua dos equipamentos para avaliar suas condições reais, utilizando tecnologias como sensores, termografia e análise de vibrações. Por meio da coleta de dados, a equipe de manutenção pode determinar exatamente quando um equipamento precisa de intervenção, evitando assim paradas não programadas e melhorando a eficiência da operação. Essa abordagem possibilita não apenas uma gestão mais eficiente dos ativos, mas também a identificação de problemas antes que se tornem sérios.
Outra técnica bastante eficaz é a manutenção preventiva planejada. Este método implica executar atividades de manutenção em intervalos programados, baseando-se em recomendações do fabricante ou na experiência da equipe de manutenção. A manutenção preventiva é projetada para evitar falhas e aumentar a vida útil dos ativos. Para que a manutenção preventiva seja eficaz, é importante que exista um calendário bem definido e que as atividades sejam registradas de maneira sistemática. A comunicação entre as equipes de operação e manutenção é fundamental para garantir que as manutenções não impactem a produção e estejam alinhadas com as necessidades do negócio.
A análise de falhas é outra técnica crucial no planejamento de manutenção. Essa abordagem envolve a investigação das causas dos problemas e falhas de equipamentos, permitindo que as equipes aprimore suas estratégias de manutenção. Realizar uma análise de falhas aprofundada ajuda a identificar padrões e a implementar ações corretivas que evitem a recorrência do problema. Essa técnica não só contribui para um planejamento de manutenção mais estratégico, mas também para um entendimento mais abrangente do comportamento dos ativos.
A metodologia 5S também pode ser aplicada no planejamento de manutenção. Originalmente desenvolvida como uma técnica de organization e limpeza, o 5S (Seiri, Seiton, Seiso, Seiketsu e Shitsuke) promove a organização do ambiente de trabalho de forma que os equipamentos estejam sempre em condições ideais. Implementar essa técnica ajuda a identificar problemas de manutenção de forma mais rápida e a manter os ativos em condições de operação eficiente. A prática do 5S pode transformar o ambiente de trabalho, facilitando a execução de atividades de manutenção e aprimorando o desempenho da equipe.
Os diagramas de Pareto, também conhecidos como a regra 80/20, podem ser uma ferramenta efetiva na priorização das atividades de manutenção. Essa técnica sugere que 80% dos problemas são causados por 20% das causas. Identificando os principais problemas com os quais a empresa lida, as equipes podem concentrar seus esforços nas áreas que terão o maior impacto. Essa abordagem não apenas melhora o planejamento de manutenção, mas também resulta em uma gestão mais eficaz de recursos e tempo.
A utilização de software de gestão de manutenção, como os Enterprise Resource Planning (ERP) e Computerized Maintenance Management Systems (CMMS), também é uma técnica que pode transformar o planejamento de manutenção. Essas ferramentas ajudam as empresas a centralizar suas informações sobre ativos, atividades de manutenção e histórico. Integrar o planejamento da manutenção ao software CRA, por exemplo, permite que as equipes acompanhem o desempenho dos equipamentos e analisem dados em tempo real, tornando o processo de tomada de decisão mais eficiente.
O planejamento por TPM (Total Productive Maintenance) é uma abordagem que envolve todos os colaboradores, visando manter a eficiência do equipamento e aumentar a produção. O TPM foca na capacitação da equipe de operação, garantindo que eles entendam e pratiquem boas práticas de manutenção. Isso não apenas melhora a responsabilidade em relação aos ativos, mas também promove uma cultura de excelência e compromisso com a manutenção dentro da empresa.
Por fim, a treinamento e capacitação da equipe são essenciais para um planejamento de manutenção eficaz. Garantir que a equipe esteja bem treinada em técnicas de manutenção e em como operar equipamentos corretamente é fundamental para a execução bem-sucedida do planejamento. Realizar treinamentos regulares e compartilhar conhecimentos sobre novas tecnologias e métodos de manutenção pode ajudar a aumentar a eficiência operacional e a reduzir erros.
Em resumo, as técnicas para planejamento de manutenção variam de acordo com as necessidades e características de cada empresa. Adotar um conjunto diversificado dessas técnicas garante uma abordagem robusta e eficaz na gestão dos ativos. Ao implementar métodos como a manutenção baseada em condição, análise de falhas, metodologia 5S e a utilização de software de gestão, as empresas estarão melhor equipadas para maximizar a eficiência operacional, garantir a segurança e reduzir custos. Uma abordagem proativa ao planejamento de manutenção é, sem dúvida, um investimento valioso que pode resultar em resultados significativos para o sucesso organizacional.
Impacto da Manutenção na Produtividade
A manutenção desempenha um papel crucial em qualquer setor industrial, influenciando diretamente a produtividade e a eficiência operacional. Uma gestão de manutenção eficaz não só garante que os equipamentos funcionem segundo suas especificações, mas também que as operações da empresa aconteçam sem interrupções. Neste artigo, vamos examinar como a manutenção impacta a produtividade e por que investir em melhores práticas de manutenção é essencial para o sucesso organizacional.
Um dos efeitos imediatos da manutenção é a redução de falhas e quebras inesperadas. Quando uma empresa realiza manutenções regulares, os colaboradores podem identificar e corrigir problemas antes que eles se agravem. Isso significa que a ocorrência de quebras inesperadas, que podem interromper a produção e gerar atrasos, é significativamente reduzida. Por exemplo, em uma linha de montagem, um equipamento quebrado pode causar a paralisação de toda a operação, levando a atrasos na entrega e insatisfação dos clientes. Com a manutenção adequada, esses riscos podem ser mitigados, resultando em uma operação mais fluida e contínua.
Além de evitar quebras inesperadas, a manutenção também contribui para a eficiência operacional. Equipamentos que são mantidos de forma regular tendem a operar com melhor desempenho. Por exemplo, uma máquina que é regularmente lubrificada, calibrada e inspecionada vai operar de maneira mais eficaz do que uma máquina que não recebe esses cuidados. Isso se traduz em menos energia desperdiçada e em uma produção mais consistente. Quando as máquinas funcionam de maneira ideal, a produtividade aumentará, e as empresas conseguem atingir suas metas de produção com mais facilidade.
A manutenção também impacta a qualidade do produto. Quando os equipos são mantidos adequadamente, a probabilidade de produtos defeituosos diminui. Um equipamento que não está funcionando bem pode produzir itens com especificações fora do padrão. Isso pode levar a perdas significativas, tanto em termos de tempo quanto de recursos financeiros. As empresas que garantem que suas máquinas estejam em excelente estado de funcionamento são capazes de oferecer produtos de qualidade superior, o que pode significar a diferença entre a satisfação e a insatisfação do cliente. A reputação da empresa no mercado é, muitas vezes, diretamente afetada pela qualidade dos produtos oferecidos.
A segurança no local de trabalho também é um fator que não pode ser ignorado quando se fala sobre manutenção e produtividade. Equipamentos mal conservados ou danificados podem resultar em acidentes de trabalho, colocando em risco a segurança dos colaboradores e causando interrupções nas operações. Acidentes não apenas prejudicam a moral da equipe, mas também podem gerar custos com indenizações e outras despesas relacionadas. Investir em manutenção para garantir que todos os equipamentos estejam operacionais e seguros não é apenas uma obrigação moral, mas também uma estratégia inteligente para reduzir riscos e maximizar a produtividade.
A integração de tecnologias de manutenção pode aumentar ainda mais a produtividade. Com o avanço de tecnologias como a Internet das Coisas (IoT), muitos sistemas de monitoramento permitem que as empresas realizem manutenção preditiva. Por exemplo, sensores podem acompanhar as condições dos equipamentos em tempo real, informando à equipe de manutenção quando é necessário fazer intervenções. Isso garante que a manutenção não seja realizada de forma excessiva, mas sim quando realmente necessário, economizando tempo e recursos enquanto garante que os equipamentos permaneçam em funcionamento.
Outro ponto a se considerar é o impacto da manutenção na moral da equipe. Colaboradores que trabalham em ambientes bem mantidos e organizados tendem a ser mais satisfeitos e motivados. Quando os equipamentos estão em boas condições e funcionais, os trabalhadores têm mais facilidade para realizar suas tarefas, o que melhora a produtividade e a qualidade do trabalho. Além disso, um bom ambiente de trabalho é um dos principais fatores para atrair e reter talentos na indústria. Investir na manutenção, portanto, não é apenas uma questão de preservar ativos, mas também de valorizar e motivar a força de trabalho.
A planejamento adequado da manutenção também pode contribuir para a diminuição dos tempos de inatividade. Quando as manutenções são realizadas, geralmente, fora do horário de pico ou de forma planejada, minimiza-se o impacto na produção. Criar um cronograma de manutenção eficiente que considere a operação e a demanda ajuda a maximizar a produção. Com este planejamento, as empresas podem realizar as manutenções necessárias sem comprometer o desempenho operacional.
Finalmente, ao integrar práticas de manutenção em uma estratégia de melhoria contínua, as empresas podem aumentar sua competitividade no mercado. Com uma operação mais eficiente, menos tempo de inatividade e produtos de melhor qualidade, as empresas se destacam em um ambiente comercial cada vez mais competitivo. As organizações que veem a manutenção como um investimento, não um custo, obtêm retornos significativos em termos de produtividade e crescimento.
Em resumo, o impacto da manutenção na produtividade é profundo e abrangente. Desde a redução de falhas e aumento da eficiência operacional até a melhoria da qualidade do produto e da segurança no local de trabalho, a manutenção é um pilar fundamental para o sucesso das operações industriais. Investir em práticas de manutenção robustas e proativas resulta em ambientes de trabalho mais seguros e produtivos, contribuindo para a satisfação do cliente e a sustentabilidade do negócio. Portanto, abraçar uma abordagem focada na manutenção é uma estratégia inteligente para qualquer organização que deseja permanecer competitiva em seus setores.
Erros Comuns em Manutenção Industrial
A manutenção industrial é uma parte vital da operação de qualquer empresa que dependa de maquinário e equipamentos. Apesar da sua importância, muitos erros podem ocorrer durante a execução das atividades de manutenção, impactando negativamente a eficiência, a segurança e a rentabilidade da organização. Reconhecer e evitar esses erros é fundamental para garantir que as práticas de manutenção sejam eficazes e contribuam para a otimização dos processos. Neste artigo, vamos explorar alguns dos erros mais comuns em manutenção industrial e como evitá-los.
Um dos erros mais frequentes é a falta de planejamento adequado. A manutenção sem um cronograma bem definido pode resultar em atividades impulsivas e não programadas, levando a paradas inesperadas e custos elevados. O planejamento inadequado pode criar um ciclo de manutenções emergenciais, o que é oneroso para as empresas. É fundamental que as equipes estabeleçam um calendário claro de manutenção preventiva e programem manutenções em horários que minimizem o impacto na produção. Criar um planejamento que considere as demandas da operação é essencial para garantir que todos os equipamentos sejam mantidos em boas condições e que a produção não seja afetada.
Outro erro comum é a negligência na documentação. A falta de registros adequados sobre as manutenções realizadas e o histórico de falhas pode dificultar a análise do desempenho do equipamento e a identificação de padrões de falhas. A documentação adequada é fundamental para referência futura e para que a equipe possa avaliar a eficácia das manutenções realizadas. Estabelecer um sistema de registro claro e acessível é uma maneira eficaz de garantir que todas as atividades de manutenção sejam registradas e que a equipe tenha informações claras sobre o histórico dos equipamentos.
A falta de treinamento da equipe é um fator que também pode contribuir para erros na manutenção industrial. Os colaboradores precisam estar bem treinados e capacitados para realizar atividades de manutenção de forma eficaz e segura. A ausência de treinamento pode levar a erros operacionais e riscos de segurança. As empresas devem priorizar o investimento em treinamentos regulares para sua equipe de manutenção, assegurando que todos tenham um bom entendimento sobre os procedimentos corretos de manutenção e operação dos equipamentos. Isso não apenas melhora a eficiência, mas também garante a segurança do ambiente de trabalho.
O uso inadequado de peças de reposição é um erro que pode comprometer seriamente a eficácia da manutenção. A utilização de peças não originais ou inadequadas para a máquina pode levar a falhas recorrentes e aumentar o desgaste dos equipamentos tão rapidamente quanto o uso de peças de baixa qualidade. É crucial garantir que somente peças recomendadas pelo fabricante sejam utilizadas durante os processos de manutenção. Investir em peças de qualidade não apenas aumenta a confiabilidade do equipamento, mas também contribui para a durabilidade a longo prazo.
Outro erro comumente observado é o desconsiderar a importância do feedback. Muitas vezes, as equipes de manutenção não buscam a opinião dos operadores sobre o desempenho dos equipamentos. O feedback dos colaboradores que trabalham diretamente com as máquinas é valioso, pois eles podem oferecer percepções sobre a performance e os problemas enfrentados no dia a dia. Estimular essa comunicação entre as equipes de operação e manutenção pode ajudar a identificar problemas antes que eles se tornem críticos e a implementar ajustes que aumentem a eficiência do equipamento.
A falta de monitoramento contínuo dos equipamentos é um erro que pode levar a falhas sérias. A manutenção preditiva é uma estratégia eficaz que permite monitorar o estado dos ativos e prever falhas. Ignorar a necessidade de monitoramento contínuo pode resultar em interrupções inesperadas e comprometimento da produtividade. As empresas devem considerar a implementação de tecnologias de monitoramento que permitam aos gestores acompanhar a saúde dos equipamentos em tempo real. Isso não só previne problemas, mas também fornece dados que podem ser usados para melhorar as práticas de manutenção.
A inexistência de uma cultura de melhoria contínua nas práticas de manutenção é outro erro significativo. Muitas empresas ainda adotam uma abordagem reativa em vez de proativa. Implementar uma cultura de melhoria contínua requer que a equipe esteja sempre buscando maneiras de otimizar os processos de manutenção e reduzir os custos. As práticas de manutenção devem ser avaliadas regularmente para identificação de áreas de melhoria. As empresas que não buscam inovação e melhoria em suas operações podem ficar para trás em um ambiente competitivo.
Por fim, não estabelecer métricas de desempenho para avaliar a eficácia da manutenção é um erro que deve ser evitado. As empresas precisam de indicadores claros para medir o sucesso de suas práticas de manutenção. Sem métricas, fica difícil identificar as áreas que precisam de melhoria e entender o retorno sobre o investimento em manutenção. Estabelecer KPIs (indicadores-chave de desempenho) pode ajudar as empresas a monitorar o progresso e a eficácia das ações de manutenção. Isso permitirá a otimização dos processos com base em dados concretos.
Em resumo, muitos erros podem comprometer a eficácia da manutenção industrial, incluindo o planejamento inadequado, a falta de documentação, a falta de treinamento e o uso inadequado de peças de reposição. Evitar esses erros requer um compromisso contínuo com a melhoria e a implementação de processos adequados de manutenção. Além disso, promovendo uma cultura de comunicação aberta e estabelecendo métricas de desempenho, as empresas podem garantir que suas práticas de manutenção se tornem cada vez mais eficazes e contribuições significativas para a produtividade geral e sucesso do negócio. Portanto, reconhecer e remediar esses erros é essencial para a longevidade e eficiência das operações industriais.
Tendências Futuras em Manutenção Industrial
A manutenção industrial está em constante evolução, impulsionada por novas tecnologias e mudanças nas exigências do mercado. À medida que as indústrias se tornam mais competitivas e dependentes da automação, é essencial acompanhar as tendências que moldarão o futuro da manutenção. Neste artigo, exploraremos algumas das principais tendências que estão influenciando a manutenção industrial e como as empresas podem se preparar para essas mudanças.
Uma das tendências mais promissoras é a manutenção preditiva, que vem ganhando destaque devido ao avanço da tecnologia. Utilizando sensores e dispositivos IoT (Internet das Coisas), as empresas podem monitorar o estado dos equipamentos em tempo real. Isso não apenas ajuda a identificar potenciais falhas antes que elas aconteçam, mas também permite que as equipes de manutenção planejem intervenções de maneira eficiente. A manutenção preditiva não é apenas uma ferramenta para evitar quebras, mas também para otimizar a utilização dos ativos, maximizando o retorno sobre investimento e diminuindo custos operacionais.
A implementação de inteligência artificial (IA) e aprendizado de máquina também é uma tendência crescente na manutenção industrial. Esses recursos permitem que sistemas analisem grandes volumes de dados e identifiquem padrões que podem não ser evidentes a olho nu. Por exemplo, uma IA pode prever falhas em máquinas com base em dados históricos e condições operacionais, proporcionando insights valiosos que ajudam a equipe de manutenção a tomar decisões mais informadas. O uso dessas tecnologias promete revolucionar a maneira como as indústrias gerenciam seus ativos e agendam suas manutenções.
Outro aspecto importante é a automação de processos de manutenção. Com o aumento da digitalização nas indústrias, muitos processos de manutenção estão se tornando automáticos. Isso inclui desde o agendamento de manutenções até a execução de tarefas repetitivas que, anteriormente, eram manuais. A automação não só aumenta a eficiência, mas também reduz a margem de erro humano, resultando em operações mais seguras e confiáveis. O uso de softwares de gestão de manutenção integrada (CMMS) facilita a gestão automática das atividades de manutenção, promovendo um ambiente de trabalho mais estruturado.
Além disso, a realidade aumentada (RA) está emergindo como uma ferramenta poderosa na manutenção industrial. A RA pode proporcionar informações em tempo real a técnicos durante o trabalho em equipamentos, sobrepondo dados digitais às máquinas que estão sendo reparadas. Isso pode incluir assistência de especialistas remotos e guiamentos visuais sobre como realizar reparos. A adoção da realidade aumentada pode reduzir os tempos de inatividade, aumentar a precisão nas manutenções e facilitar o treinamento de novos colaboradores.
A sustentabilidade e a manutenção verde também são tendências que estão se tornando cada vez mais relevantes. As empresas estão sendo pressionadas a adotar práticas mais sustentáveis, incluindo a manutenção. Isso envolve o uso eficiente de recursos, a minimização de resíduos e a escolha de técnicas que reduzam o impacto ambiental. Sistemas de gerenciamento de manutenção que incorporam práticas de sustentabilidade podem ajudar não apenas a cumprir normas regulatórias, mas também a melhorar a imagem da empresa no mercado. Melhorar a eficiência energética das máquinas e reduzir as emissões são passos importantes que estão alinhados com as exigências atuais.
Além disso, a integração de soluções baseadas em nuvem está simplificando a gestão da manutenção industrial. Com plataformas em nuvem, as empresas têm acesso a dados e informações em tempo real, independentemente de onde estejam. Essa acessibilidade permite uma gestão remota e a troca de informações mais fácil entre as equipes que trabalham em diferentes locais. O uso de soluções em nuvem para a gestão de manutenção pode, portanto, oferecer maior agilidade e flexibilidade, tornando as operações mais responsivas às exigências do mercado.
Uma tendência importante que não pode ser negligenciada é a importância crescente da cibersegurança. À medida que mais dispositivos estão conectados à Internet e a digitalização avança, as indústrias enfrentam novos desafios em termos de segurança de dados. As vulnerabilidades cibernéticas podem causar paralisações significativas ou até mesmo comprometer a segurança dos colaboradores e equipamentos. Portanto, as empresas devem não só focar na implementação de novas tecnologias, mas também em estabelecer protocolos de segurança robustos para proteger suas operações e dados.
A formação e capacitação da equipe de manutenção são também essenciais nesta nova era. Com a introdução de tecnologias disruptivas, é imprescindível que as equipes sejam constantemente treinadas e atualizadas sobre as novas ferramentas disponíveis. A criação de uma cultura de aprendizado contínuo permitirá que a equipe não apenas se adapte às novas tecnologias, mas também a transforme em uma vantagem competitiva para a empresa. Um investimento na formação pode resultar em maior eficiência, segurança e produtividade em todas as operações.
Em resumo, o futuro da manutenção industrial é promissor, com tendências como manutenção preditiva, inteligência artificial, automação, realidade aumentada e sustentabilidade se tornando cada vez mais relevantes. Ao abraçar essas novas práticas e tecnologias, as empresas podem não apenas melhorar a eficiência e reduzir custos, mas também garantir a segurança e a continuidade das operações. Para se manter competitivas, as organizações devem estar dispostas a se adaptar a essas mudanças e investir em suas equipes e processos. As empresas que agirem de forma proativa em relação às tendências emergentes estarão mais bem posicionadas para enfrentar os desafios do futuro e prosperar em um ambiente em constante transformação.
Em suma, a Manutenção Industrial é um elemento crucial que não pode ser ignorado por empresas que desejam maximizar sua eficiência operacional e prolongar a vida útil de seus equipamentos. A discussão sobre as diferentes abordagens de manutenção revela a variedade de estratégias disponíveis para otimizar processos produtivos. Ao implementar práticas efetivas, como a manutenção preventiva, preditiva e a utilização de novas tecnologias, as organizações podem não apenas reduzir falhas, mas também aumentar a produtividade e a segurança no ambiente de trabalho. As empresas que investem em suas práticas de manutenção não apenas asseguram a continuidade de suas operações, mas também alcançam uma vantagem competitiva no mercado. Portanto, é essencial que os gestores adotem uma abordagem proativa, garantindo que suas estratégias de manutenção estejam sempre alinhadas às exigências do setor e às inovações tecnológicas. Dessa forma, estarão preparadas para enfrentar os desafios futuros e prosperar em um cenário industrial cada vez mais dinâmico.